What is Concrete Crazing?
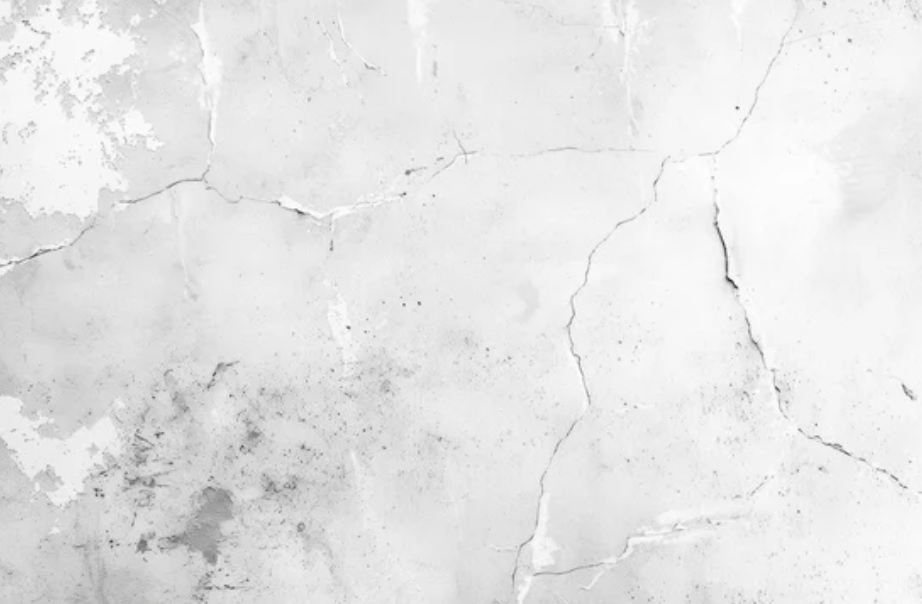
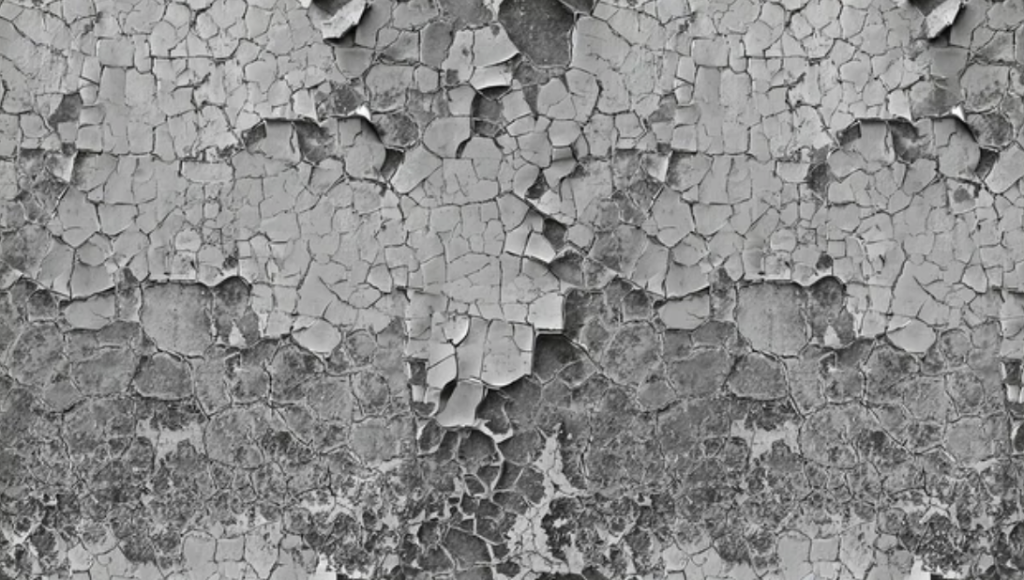
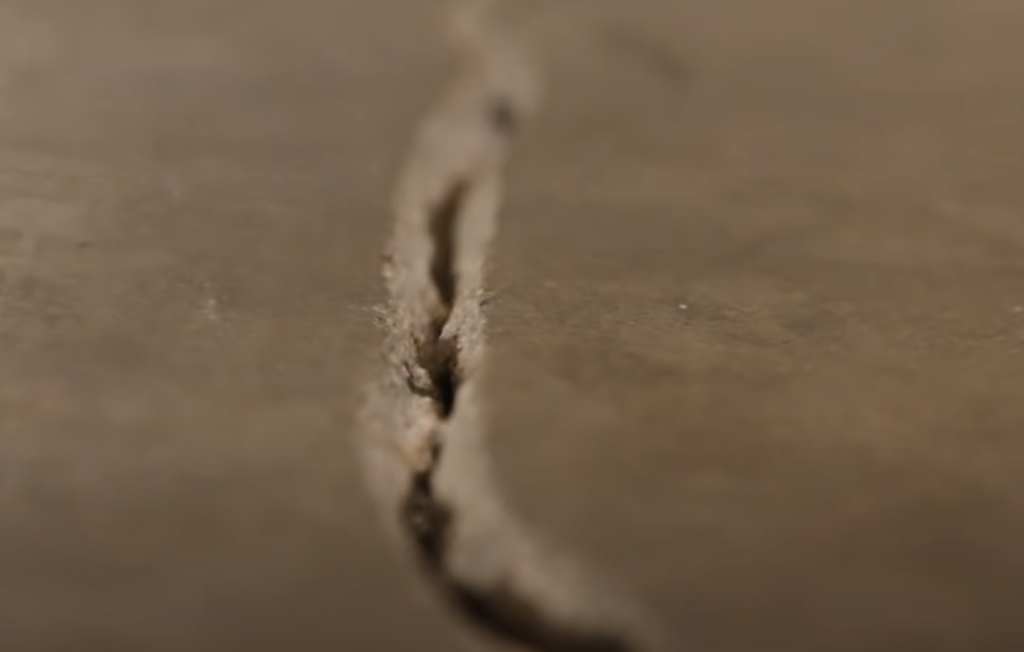
Crazing refers to the formation of a network of random cracks or fissures on the surface of concrete or mortar due to the shrinkage of the surface layer. These cracks typically do not exceed 1/8 inch (3 mm) in depth and are more prominent on surfaces that have been steel-troweled. The cracks enclose irregular hexagonal areas, generally no larger than 1 1/2 inch (40 mm) across and sometimes as small as 1/2 or 3/8 inch (12 or 20 mm) in unique cases. Typically, craze cracks appear shortly after the concrete is placed, becoming apparent either the day after placement or, at the latest, by the end of the first week. They may not be easily visible until the surface is wetted and starts to dry out.
Crazing cracks are occasionally known as shallow map or pattern cracking. Importantly, these cracks do not compromise the structural integrity of concrete and seldom impact its durability or wear resistance. Nevertheless, surfaces with crazing can be visually unappealing, particularly when concrete contains calcium chloride, a commonly used accelerating admixture.
Why do concrete surfaces craze?
Shrinkage in the concentrated dense paste layer at the surface often leads to craze cracks on hard steel-troweled slab surfaces. Additionally, failure to adhere to one or more of the “good concrete practices” can contribute to concrete surface crazing. The primary factors contributing to crazing include inadequate curing and environmental conditions that promote high evaporation rates. These conditions, such as low humidity, extreme ambient temperatures, direct sunlight, and drying winds, accelerate surface drying when the concrete is in the early stages of gaining strength, leading to rapid surface drying and the formation of craze cracks.
Excessive wetness in the mix, prolonged floating, the utilization of a jitterbug, or procedures that depress the coarse aggregate and lead to an undue concentration of cement paste and fines at the surface can all contribute to issues. Performing finishing operations while there is still bleed water on the surface or using a steel trowel in a manner that brings up excessive water and cement fines due to its smooth surface can also be problematic.
The use of a bull float or darby with water on the surface, especially while the concrete is still bleeding, creates a high water-cement ratio at the surface. This results in a weakened surface layer that is prone to crazing, dusting, scaling, and other surface defects. Sprinkling cement on the surface to accelerate the drying of bleed water is a common cause of crazing, as it concentrates fines on the surface. Similarly, spraying water on the concrete surface during finishing operations can lead to a weakened surface that is susceptible to crazing or dusting.
How to prevent Crazing?
While many contractors advertise a concrete driveway or patio removal cost ranging from $2 to $6 per square foot, it’s important to note that for smaller sections of your driveway or patio, they may impose a project minimum. This minimum amount is designed to make the effort financially viable for them.
This implies that even for very modest projects, you could end up paying around $1,000 to have professionals handle the concrete demolition and disposal for you.
To prevent crazing, initiate concrete curing promptly. Curing is crucial for maintaining the necessary moisture for the proper reaction of cement with water, known as hydration. Keep the surface consistently wet by either flooding it with water or covering it with damp burlap for a minimum of 3 days.
Another option is to apply a liquid-membrane curing compound to the surface. Avoid subjecting concrete surfaces to alternate wetting and drying in the early stages. During placement, use concrete with a moderate slump (3 to 5 inches [75 to 125 mm]). Higher slump (up to 6 or 7 inches [150 to 175 mm]) can be employed if the mixture is designed to achieve the required strength without excessive bleeding and/or segregation, typically achieved through the use of water-reducing admixtures. Never sprinkle or trowel dry cement or a mixture of cement and fine sand onto the plastic concrete surface to absorb bleed water.
Avoid sprinkling water on the slab to aid in finishing. If needed, remove bleed water by dragging a garden hose across the surface. Do not perform any finishing operations while bleed water is still present.
To counteract high evaporation rates, moisten the subgrade lightly before placing the concrete to prevent excessive absorption of water from the concrete. If a vapor retarder is necessary for the subgrade, overlay it with 3 to 4 inches of a compactible, granular fill, like crusher-run material, except in cases where the slab will have a vapor-sensitive floor covering or will be situated in a humidity-controlled environment. Refer to CIP 29 for information on the placement of vapor retarders.